Dee Bus Service
Customer Spotlight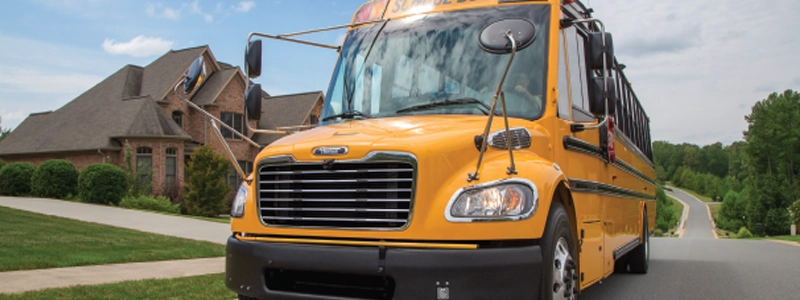
Safer students, healthier buses, thousands in yearly savings: This contract school bus fleet has it all.
Family owned school bus contractor, Dee Bus Service, Inc. (DBSI) serves 57 school districts across three counties in the Boston/Metrowest area.
The company’s 238 school buses and 130 vans stay deployed to districts’ lots instead of being parked in a single location each night. However, DBSI is still responsible for vehicle health and required inspections.
They realized that they could streamline operations and reduce costs with modern smart fleet management and electronically verified inspections.
- Operations would be more effective with greater visibility
- Vehicles would be inspected and serviced faster.
- Maintenance expenses would be reduced by proactively addressing frequent issues.
Technology Administrator Craig Lussier contacted us after one of DBSI’s leadership team gave him a Zonar business card asking to reach out and see if Zonar is the right fit for us. In October 2018, we worked with Craig to launch a pilot of Zonar Ground Traffic Control, Zonar V4 TCUs and Zonar EVIR. In December, we became DBSI’s provider and partner and began expanding the implementation.
EVIR saves time, effort and $7,000 a year.
Before using EVIR, drivers used paper-based DVIR books for vehicle inspections. Up to two weeks could pass from defect discovery to repair.
- One week to visit the depot, collect and review reports, and prioritize repairs.
- Another week to travel to back to the vehicle and perform needed repairs.
Some vehicles broke down because the defect grew critical while awaiting repair. When these failures occurred during routes, more time and money were lost to breakdowns, substitutions and towing.
Now vehicles are serviced in 2 days or less.
Drivers now use EVIR to perform electronic inspections, fast and efficiently.
- They physically visit each inspection zone.
- They follow the process displayed on their Zonar tablet.
- And they upload the results to Ground Traffic Control for remote review.
Each inspection report is immediately available online, eliminating the need to travel, collect and sift through paper forms. And repairs are performed in one to two days, not weeks.
- Vehicles are serviced in 24 to 48 hours.
- Eliminating DVIR books saves more than $7,000 a year.
- Major repair costs have declined.
- Towing expenses are now next to zero.
- Vehicles are better maintained, healthier and retaining a higher resale value.
Mechanics know exactly where to go.
As a contracted fleet, DBSI buses and vans stay deployed. Before using Zonar GPS, finding the vehicle could extend the time it took mechanics to arrive, which extended the service window and delayed repairs.
Now, the V4 TCU on each bus and Zonar LD TCU on each van provides real-time locations. Authorized personnel now locate any tracked fleet vehicle online or using the mobile app to view the map in Ground Traffic Control. Mechanics also know exactly where to travel, in real time, to service the fleet out on the road.
Modern tech streamlines shop workflows.
DBSI has replaced its antiquated preventative maintenance solution with an in-house program that takes advantage of the vehicle data captured in Ground Traffic Control. Drivers perform their EVIR inspection using their Zonar tablet. Maintenance staff then logs in to their Ground Traffic Control account to identify buses needing service.
In both cases, the vehicle’s VIN, type, make, model, mileage (and more) are already populated. Fewer fields to enter. And the workflow is streamlined.
When mechanics service the vehicle, a record of that work is available for staff and drivers
Digital records comply without adding physical storage costs.
U.S. DOT regulations require that two years of inspection data be stored. Digitizing inspection and vehicle records using Ground Traffic Control means that each day, DBSI moves away from physical storage costs for paper forms.
Dead batteries drained resources.
Many of DBSI’s newer school buses don’t have an alarm that sounds when their headlights are left on or keys are left in the ignition. One mistake, especially overnight or before a vacation week, meant drained bus batteries for the next route.
With buses deployed and stored in districts’ lots across a wide geographic area, replacing a dead battery first thing in the morning wasn’t easy.
- Available spare batteries became hard to find, especially in that lot.
- Hard dollar costs added up as DBSI replaced drained and dead batteries.
- Switching buses early mornings puts drivers behind schedule for the rest of that scheduled run.
Having multiple buses with drained or dead batteries at the same time compounded the problems.
Dispatching multiple teams at the same time, as well as pulling them from scheduled repair and maintenance schedules, puts the garage behind. And results in longer than normal repair times along with asset schedule changes.
Low voltage alerts protect students and service.
Zonar smart fleet management provides remote, real-time insight into vehicle health, including battery voltage levels. And supports alerts when a diagnostic issue is detected.
- The V4 detects the battery’s low voltage level.
- Ground Traffic Control issues a low voltage alert.
- DBSI addresses the issue, protects service levels and reduces expenses.
Best of all, reliable batteries and healthier buses leave fewer students needing a roadside transfer on their way to school. Safer for everyone.
Insight exonerates drivers’ braking habits.
Zonar diagnostics provide a real-time solution to help DBSI mechanics know what may be going on with a V4- or LD-equipped asset in trouble. They respond proactively based on the data in Ground Traffic Control or its mobile app.
When an asset is just starting to have a mechanical issue that could lead to a breakdown or failure, DBSI is already ahead of the curve instead of reactively trying to catch up.
Ground Traffic Control data also showed that hard braking events were rare throughout the fleet overall; drivers were braking safely. Instead, DBSI learned that upgrading from factory installed components during routine preventative maintenance schedules extended brake life and reduced expenses long term.
Higher quality tablet docks increased savings.
Initial installation of new Samsung Tab Active3 tablets enhanced the driver experience. But DBSI had concerns about the first design of the tablets’ docking stations. The design wasn’t user friendly for daily use, which caused communication and charging issues between the docks and the tablets.
We partner with RAM Mounts, a leader in rugged tablet mounts. This partnership offered a pilot a their tablet docks, which became the standard for the fleet’s tablet docks to date.
- Proved more durable.
- Reduced replacement costs.
- Enabled faster EVIR Inspection times.
Future maintenance efficiency is in works.
In the coming year, DBSI will add a Maintenance tab within the EVIR online portal to enable more efficient maintenance management.
- Track all maintenance repairs and service calls in real time, while in the field.
- View any and all work done on any asset, including when, where and by who.
- Reduce number of steps for viewing an asset’s performance and repair history to a few simple keystrokes.
All of this information will be automatically captured and logged when the maintenance associate logs in to their tablet and performs the necessary work.
Black tags will remain the same to identify the asset and its relevant information. Drivers will see what they’re looking for before or after a trip for defects or necessary repairs.
Marigold zone tags around the asset have a different set of parameters. Maintenance will see what they’re repairing or general maintenance concerns.
Once the repair work is entered into EVIR, and performed and closed out on tablet, the maintenance associate will log in to Ground Traffic Control and close the completed tasks.
Repair and maintenance work records will be stored—by asset—in the new Maintenance tab, where they’ll be reviewed, stored and printed as needed. Simple as that.
Support and communication, together.
Lussier works with Zonar Senior Director of Customer Support and Experience, Bobby Smith; winner of the 2023 Business Intelligence Group’s Executive of the Year for Excellence in Customer Service.
He appreciates Bobby’s dedication to DBSI’s success on a one-on-one level. Lussier and Smith share thoughts and work through concerns that arise during their collaboration and partnership.
Both have worked on multiple V4 Thomas Fleet projects together and tirelessly on the Zonar LD to ensure the best-of-market GPS solutions for every Zonar customer, not just DBSI. Both know they’re just an email or phone call away if needed. And they rely on each other’s honest opinions and investment in each other’s roles as leaders in transportation solutions.